Despite what is undoubtably very clever and complex engineering, the Double (or Dual) Clutch Transmission (DCT), has a mixed reputation with drivers and has not achieved the level of ubiquity many thought it would.
Sitting in the middle ground between an automatic and a manual transmission, the simplest way of describing their operation, is that they’re an automatically operated manual transmission – achieved by using two clutches.
Jan 03, 2020 A dual-clutch transmission is one approach to an automatic transmission. Think of it as a manual transmission controlled by a computer, but instead of one clutch, it has two. One clutch controls the even gears, and the other controls the odd gears. Ford’s dual-clutch transmission, code-named DPS6 and used in its Fiesta and Focus, has been troubled for years. It’s the subject of a potential $4 billion lawsuit. It had Ford secretly telling.
- Dual Clutch Transmission. With our automatic DCTs, one clutch is engaged with the current gear while sensors predict whether the next gear change will be an upshift or downshift. The second clutch prepares the next gear ratio for instant engagement with a negligible loss of torque. Our 8-Speed DCT includes a torque converter to smooth low-speed.
- DCT stands for Dual Clutch Transmission, but that alone doesn’t fully explain it. A DCT is a type of Automated Manual Transmission (AMT) that has two clutches instead of just one.
Doing away with the torque converter of a normal automatic transmission, they utilise the traditional gearing methods of a manual - but then split that gearing across two output shafts to allow power flow to shift between them incredibly quickly.
ORIGINS
Also referred to as a Direct Shift Gearbox (DSG), most car manufacturers have their own version or versions, but use them selectively across their ranges of vehicles – with the Volkswagen group the most invested in their implementation.
Like so many ‘new’ developments for automobiles, the double clutch transmission is an idea that had been around for a significant amount of time before finally being put to use, having been experimented with pre-World War two.
Its realisation had to wait until the 80’s, and it was Porsche who eventually became the first major adopter having worked on their own version since the 60’s.
The Porsche 956 released in 1983 received the distinction of being the first to feature one, and their complexity and expense kept them in the realm of motor racing and high-end super cars for the most part.
Space was also a considerable restriction. The electronics needed for the computerised control module had not yet reached the miniaturisation levels of modern times and so were quite sizeable and took up valuable engine bay space.
It wasn’t until 2003 that a production road car featured a DCT, in Volkswagen’s Mk4 Golf R32.
ADVANTAGES
The purpose behind a DCT is to reduce the gap between gear shifts to a minimum, with the benefits being improved performance and fuel efficiency. Copyright free football highlights.
Sofia font family. The less time spent off the power changing gear during acceleration the faster the vehicle can accelerate - and by reducing the time spent off the power during gear changes in general, the better fuel economy will be as engine power isn’t wasted.
Gear changes on DCTs can now be measured in the milliseconds, faster than any driver is capable of, and still retain the advantages a manual gearbox has over an automatic.
How it achieves these lightning fast changes is by anticipating what the next gear needed will be, based on factors such as rate of acceleration or deceleration, current speed of travel and engine speed.
This allows the computer to have the predicted gear already engaged before the change is made.
OPERATION
Unless you’re already familiar with how a DCT works, you’re probably already questioning how this type of transmission can have two different gears selected simultaneously without exploding into a shower of shrapnel.
The clue is in the name but that’s only describing part of the process. Yes, there are two clutches, but simply having an extra clutch doesn’t really explain how a transmission can select more than one gear at a time.
The twin clutches are arranged concentrically – meaning one sits within the circumference of the other, crucially enabling them to both work on the same input shaft.
However, the input shaft connected to both the clutches is not one shaft, but two - with one of them sitting within the other and allowing each clutch to contact and act upon a different one.
The gears are split across the split input shaft by odds and evens, allowing the transmission to switch back and forth between them as the car accelerates and decelerates – pre-selecting each gear on the opposite input shaft to the one engaged.
The gears themselves are no longer engaged purely mechanically by the gear level either and are instead actuated by shift forks powered by pistons, engaging and disengaging as necessary.
When you shift gears, the gear level is signalling for these pistons to actuate and engage the synchronisers onto the chosen gear, and not mechanically engaging them itself.
In this simplified diagram you can see how the input shaft is divided in two via a hollow shaft, with one running through the other and both controlled by the double clutch switching between them.
The gears work as a normal synchromesh transmission would, by utilising synchronisers to connect the gears to the output shafts.
Tracing a line from the blue clutch on the left, along the input shaft, up onto first gear on the first output shaft, and then continuing along and down onto the transmission output gives you first gear.
While this is happening, the computer is deciding which gear you’ll be wanting next. If you are accelerating it will almost certainly opt for second gear and connect this gear on other half of the input shaft so that it is ready as soon as you want to shift up into second.
On shifting, the clutches switch over and power transfers to the grey section of the input shaft, tracing a line along and down onto second gear and out onto the transmission output as before.
There’s a slight overlap between the two as the clutches engage and disengage, but the change is incredibly fast with almost no gap between the two speeds, giving the impression of a near seamless gear change.
It’s a very sophisticated system - but not one without its problems or detractors.
PROBLEMS
The system does run into problems when going from stationary to very slow speeds, where there’s a delay in engaging first gear but the driver is still depressing the accelerator waiting for power delivery. Once the system catches up and the gear is engaged, the car will then accelerate according to how fast the engine speed is - and if the driver has given it too much power it can cause the car to shoot forwards unexpectedly.
This problem can be largely attributed to unfamiliarity with the system, but other complaints are more directly related to its mechanical processes - although this is usually relevant for earlier model DCT/DSGs.
These include having to wait for the system to shift down gears when decelerating rapidly, as it is unable to skip gears due to the alternating method of operation between input shafts; and problems with reversing up hills where the system can get confused by which gear it should be engaging next.
Like any system, continued refinement and improvement eliminates problems and improves operation, and this could be the case here if given the development time. However, the writing could already be on the wall as some automotive manufacturers have already cast doubt over the future of the complex transmissions.
Advances made in automatic transmission technology have closed the gap to DCT/DSGs, and with automatics already selling in increasing numbers over manuals we could well see a time in the near future where manual transmissions phase out completely – leaving them to the enthusiasts.
MAT FOUNDRY GROUP ARE A LEADING MANUFACTURER OF GREY AND DUCTILE IRON CAR COMPONENTS. TO LEARN MORE ABOUT US VIEW OUR PRODUCTS OR CONTACT US TODAY
Double-clutching (also called double de-clutching in countries outside of the United States) is a method of shifting gears used primarily for vehicles with an unsynchronized manual transmission, such as commercial trucks and specialty vehicles. While double clutching is not necessary in a vehicle that has a synchronized manual transmission, the technique can be advantageous for smoothly upshifting in order to accelerate, and when done correctly it prevents wear on the 'synchros' which normally equalize transmission input and output speeds to allow downshifting.
With this method, instead of pushing the clutch in once and shifting directly to another gear, the driver first engages the transmission in neutral before shifting to the next gear. The clutch is depressed and released with each change.[1] A related downshifting/rev-matching technique is heel-and-toe shifting, in which the throttle is blipped (i.e. momentarily opened while engaged in downshifting) by the driver's heel. The driver's toes will accomplish the braking as the clutch is depressed, causing the engine speed to rise and closely match the transmission speed enabling smooth performance downshifts. These two techniques can be combined, e.g. using the 'toe' to brake to slow the car while entering a corner, while using the heel to press the throttle pedal for the double-clutch technique. In this manner, one may downshift and brake at the same time, and be ready to accelerate again once the corner is completed.
Technique[edit]

The double-clutching technique involves the following steps:
- The accelerator (throttle) is released, the clutch pedal is pressed, and the gearbox is shifted into neutral.
- The clutch pedal is then released, the driver matches the engine speed to the gear speed either using the throttle (accelerator) (when changing to a lower gear) or waiting for engine speed to decrease (when changing to a higher gear) until they are at a level suitable for shifting into the next gear (although double clutching is almost always used for downshifting only).
- At the moment when the revs between the input shaft (i.e. engine revs) and gear are closely matched, the driver then presses the clutch again and shifts into the next gear. The result should be a very smooth gear change.
Manual transmission shifting[edit]
In a gearbox with neutral between gears, a typical shift actually involves two gear changes, once into neutral, and again into the next gear. During any shift, disconnecting drive components via a clutch unloads the engine and transmission of the force from the opposing components. Using the clutch for each shift out of, and then into, each gear is double clutching or declutching. Due to the absence of a neutral spacing, double-clutching is impossible for sequential gear changes, as with a fully sequential gearbox used in motorcycles and racecars.
History and theory[edit]
Before the introduction of transmission synchronizers (in the 1920s), double clutching was a technique required to prevent damage to an automobile's gearing during shifts. Due to the difficulty and most often unnecessary redundancy involved in the technique, coupled with the advent of synchronized gearing systems, it has largely fallen into disuse. However, drivers of large trucks often use the double clutching technique when unable to keep the transmission unloaded during shifting, as large vehicles are (or were) usually equipped with older, simpler, and more durable unsynchronized ('crash') gearboxes.
The purpose of the double-clutch technique is to aid in matching the rotational speed of the input shaft being driven by the engine to the rotational speed of the gear the driver wishes to select. The output shaft in the transmission is directly driven by the rotating wheels, and each gear set is a different ratio, so in a five-speed transmission in fourth gear, one will have three lower gearsets not engaged spinning at three different, and faster, rates and one higher gear spinning at a slower rate than the input shaft. In order to shift down, fourth gear has to be disengaged, leaving no gears connected to the input shaft. This is neutral, and the input shaft and gears all need to be accelerated so the speed of the output shaft and the lower gear the operator wishes to select match speeds long enough for the dog clutch to lock them together. When the speeds are matched, the gear will engage smoothly and no clutch is required. If the speeds are not matched, the dog teeth on the collar will 'clash' or grate as they attempt to fit into the holes on the desired gear. A modern synchromesh gearbox accomplishes this synchronization more efficiently. However, when the engine speed is significantly different from the transmission speed, the desired gear can often not be engaged even in a fully synchronized gearbox. An example is trying to shift into a gear while travelling outside the gear's speed or directional range, such as accidentally into first from near the top of second, or intentionally from reverse to a forward gear whilst still moving at speed.
Double clutching, although (slightly) time consuming, eases gear selection when an extended delay or variance exists between engine and transmission speeds, and reduces wear on the synchronizers (or baulk rings), which are brass cone clutches themselves, and wear very slightly each time they are used to equalize the transmission revs with the output revs.
One can 'rev match' the same way without declutching the first time to take the transmission out of gear; as long as it is not under load. A transmission can usually be pulled out of gear and into neutral without significant difficulty, and then the operator can match revs, clutch and engage gear in the same manner as previously described. The first declutching is simply to ease taking the transmission out of gear. It is also possible to rev match and shift into a lower gear without using the clutch at all, but unless one is very skilled and practiced, this will generally take a lot of material off the synchronizers or grind gears excessively until it gets into gear (with unsynchronized transmissions). Provided one correctly matches the revs, a transmission can be shifted into gear quite easily without any clutch, but this is usually best left for emergencies only, for the average automobile driver.
Although double clutching is a testing requirement when obtaining a commercial driver's license, most experienced truckers learn to shift gears without using the clutch. This is known as floating gears or float shifting, with the clutch needed only during starting and stopping.
Conversely, in order to shift down, engine speed must be increased while the gearbox is in neutral and the clutch is engaged. This requires the driver to slow the vehicle sufficiently, shift into neutral, apply throttle to bring the rpm up to a suitable speed, and finally shift into gear. This operation can be very difficult to master, as it requires the driver to gauge the speed of the vehicle and throttle to the intended gear accurately; vehicle weight and road gradient are important factors as they influence the vehicle's acceleration or deceleration during the shift.
Sometimes, truck drivers use the engine brake to help match the engine speed to the gear. The most common situation is with a loaded vehicle which has no split gears or half gears in the lower range, from gears 1–4. In this case, it is especially difficult and sometimes impossible to get from 1 to 2, and sometimes even from 2 to 3 while starting on a hill. The problem is that by the time the engine speed has dropped sufficiently to enable a shift into the higher gear, the vehicle will have slowed down too much or possibly even stopped, making the shift impossible. The engine brakes, which on some models can be set to different intensities (retarding variable numbers of engine cylinders) enable a shift by dropping the engine speed quickly enough to catch the higher gear before the vehicle has decelerated too much. This technique, sometimes called 'jake shifting', requires high skill and much practice shifting without the clutch, and is usually not recommended among truck drivers because mistakes can cause damage to the transmission. Some authorities prohibit jake shifting.
References[edit]
- ^'Double-Clutch'. Dictionary.com. Retrieved August 9, 2012.CS1 maint: discouraged parameter (link)
External links[edit]
- 10 Speed Shifting TIPS, 2018 – Truck Driver Students, YouTube, 29 September 2016 (double clutch, finding gears, slow down gears on stopped vehicles)
- What's All This Double-Clutching Stuff, Anyhow? (another detailed description and reasons for double clutching)
Hyundai Double Clutch Transmission
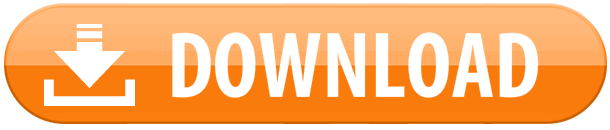